-
Capacity8-176t/d
-
Feed Size≤30mm
-
Output Size1.6-0.023mm
-
Applicable MaterialsGypsum
Application of Gypsum Powder
Gypsum powder is a common building material whose main component is calcium sulfate and has the following uses:
- Building materials: Gypsum powder can be used to make gypsum boards, gypsum blocks, ceilings, partition boards and other building materials.
- Sculptures and crafts: Gypsum powder can be used to make sculptures, models, toys and other crafts.
- Medical uses: Gypsum powder can be used to make medical supplies such as plaster bandages and dental models.
- Industrial use: Gypsum powder can be used to make molds, casting models, ceramic molds and other industrial supplies.
- Agricultural uses: Gypsum powder can be used to improve soil, adjust pH, increase soil fertility, etc.
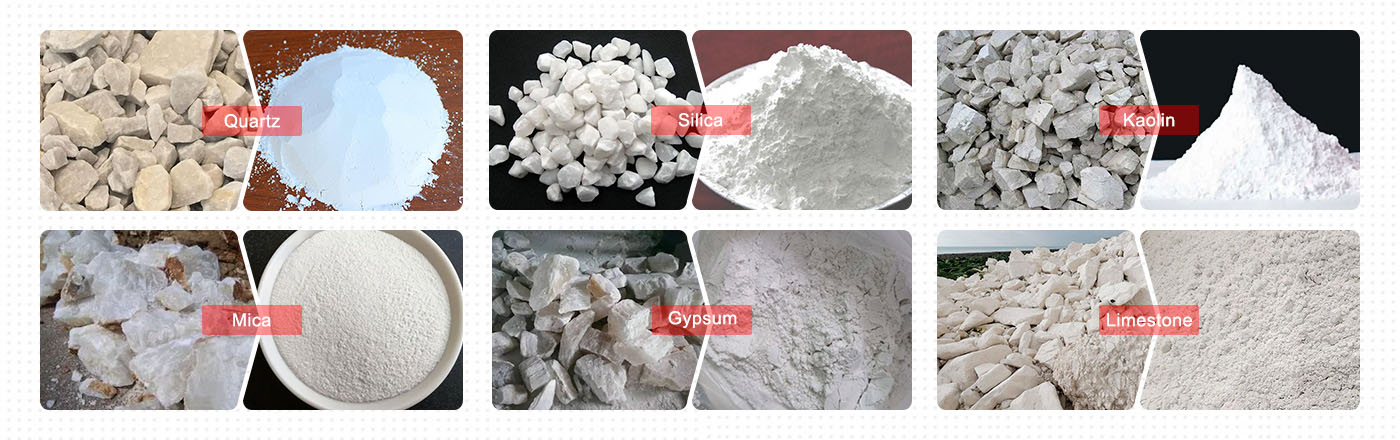
The production process of gypsum mortar powder involves multiple steps to ensure quality and efficiency from raw materials to final product. The following is the main process flow of gypsum powder manufacturing:
Crushing: First, the gypsum ore is screened and crushed to ensure that its particle size meets production requirements. Ore with a particle size greater than 20mm will be crushed and screened again.
Grinding:Gypsum ore needs to be ground into fine gypsum powder.
Calcination Dryer: Finely ground gypsum ore enters The calcining kiln performs the calcining process. The calcination temperature is usually controlled between 140℃~180℃, and the duration is about 5~6 hours. During this process, the moisture in the gypsum ore is removed to obtain gypsum semi-finished products.
Cooling:The calcined material enters the cooler to ensure the quality of gypsum powder.
Finished product packaging:The gypsum powder enters the packaging machine through the conveying device for packaging
If the water content is too high, it must be dried before grinding. The main processes are crushing, drying, grinding, and packaging of finished products. This type of gypsum powder can be used in gypsum mortar, plastering gypsum, papermaking gypsum and other fields, gypsum board and other building materials, and putty powder.
Product Features
High grinding efficiency and convenient fineness adjustment
It has the advantages of continuous production, large production capacity, high grinding efficiency, vertical cage separator head, uniform fineness of finished products, easy to adjust fineness and small energy loss.Strong adaptability
Strong adaptability to materials, can grind a variety of Mohs hardness is not greater than 7 non-metallic ores.Green environment protection
Pulse dust collection system, strong dust cleaning effect, all the positive pressure parts of the main engine are sealed, basically realize no dust processing workshop.Fewer transmission parts, low maintenance costs
The equipment has compact structure, less transmission parts, low maintenance cost, stable operation and easy installation.Working Principle
Gypsum grinding mill workflow
1.After big block be crushed into small particle by the jaw crusher.
2.Fall into the silo through the bucket elevator,The electric magnetic vibrating feeder under silo evenly feed the material into the Raymond mill to grinding according to the set quantity of flow.
3.When the main machine of the Raymond mill is working, the grinding roller rolls tightly on the grinding ring under the action of centrifugal force. The material is scooped up by the shovel and sent to the middle of the grinding roller and the grinding ring. The material is broken into powder under the action of the grinding force. Then, under the action of the fan, the powdered materials are blown up and passed through the analyzer. The materials that meet the fineness requirements pass through the analyzer. The materials that do not meet the requirements are returned to the grinding chamber to continue grinding.
4.The qualified material go into the double cylone powder collector with the airflow,then transport to the discharge hole by the discharge screw, the excess air suction into pulse dust collectorby the negative pressure fan and discharge after reach the standard of the dust remove .
5.The finnal products transport to the cylinder silo by Pneumatic transmission device.
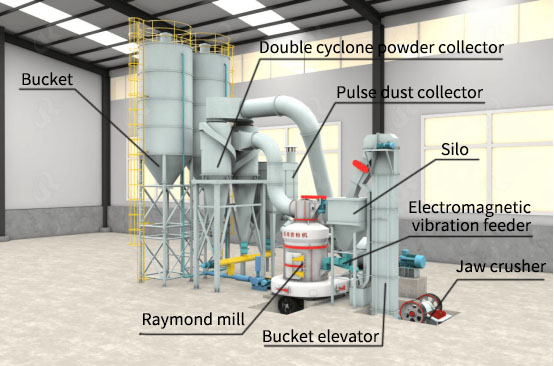
Technical Parameter
Model | KL500 | KL650 | KL780 | KL980 | KL1100 | KL1450 | KL1760 | KL1950 | KL2100 |
Handling Ability (t/h) | 0.5-2 | 0.5-2.5 | 1-3 | 1.5-4 | 2-6 | 6-10 | 8-20 | 15-30 | 20-40 |
Main Motor Power(kw) | 7.5 | 15 | 18.5 | 30 | 45 | 90 | 132 | 185 | 220 |
Fan power(kw) | 5.5 | 11 | 15 | 22 | 37 | 90 | 132 | 185 | 220 |
Analyst power(kw) | 1.1 | 1.1 | 2.2 | 2.2 | 5.5 | 7.5 | 22 | 37 | 45 |
Rotate Speed(r/m) | 120 | 120 | 120 | 120 | 120 | 90 | 90 | 90 | 90 |
Diameter of Grinding Ring(mm) | 500 | 650 | 780 | 980 | 1100 | 1450 | 1760 | 1950 | 2100 |
Diameter of Grinding Roll(mm) | 150 | 180 | 260 | 300 | 320 | 400 | 450 | 570 | 630 |
Maximum Feed(mm) | 15 | 15 | 15 | 20 | 25 | 30 | 30 | 40 | 40 |
Finished Particle Size(mm/mesh) |
1.6 ------ 0.045mm (16-325 Mesh) |
1.6------0.023mm (16-600mesh) |
|||||||
Weight(t) | 1.8 | 2.8 | 3.8 | 6.5 | 14.5 | 26 | 48 | 65 | 85 |
Company Profile
Kolev Equipment Technology Co., Ltd. is a large-scale private technology enterprise. The company is committed to the research and development, production and sales of technical equipment for the mining and metal ore industries. It has been deeply involved in the ultra-fine grinding, industrial drying and crushing sand making industries for many years. We can provide you with Provide intelligent solutions and mature supporting products, focusing on the development of various powder equipment, complete powder production lines, drying production lines, sand and gravel line equipment and projects.Products are sold to 160 countries and regions and are well received by customers.
Kolev Equipment has always been adhering to the business philosophy of surviving by quality and developing by credibility, striving to win the trust of customers with high-quality products and perfect after-sales service, and create a brilliant future for Kolev.
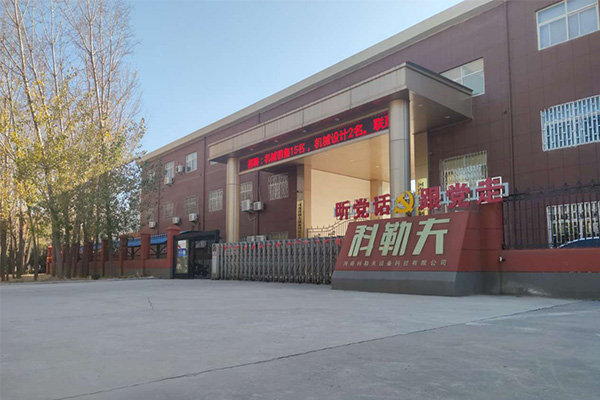
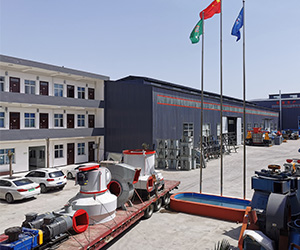
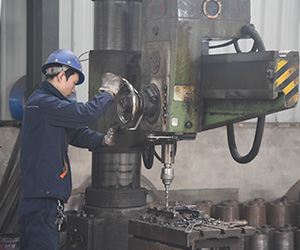
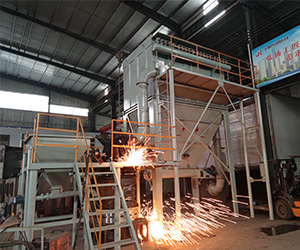
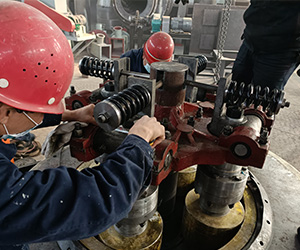
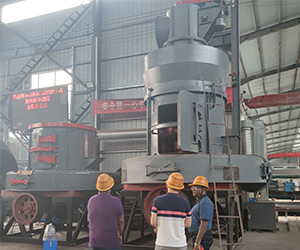
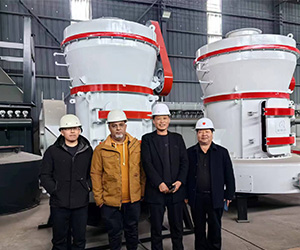
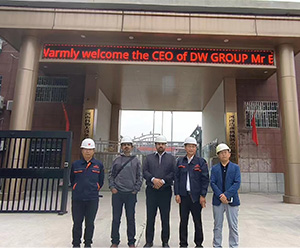
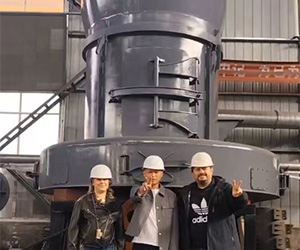
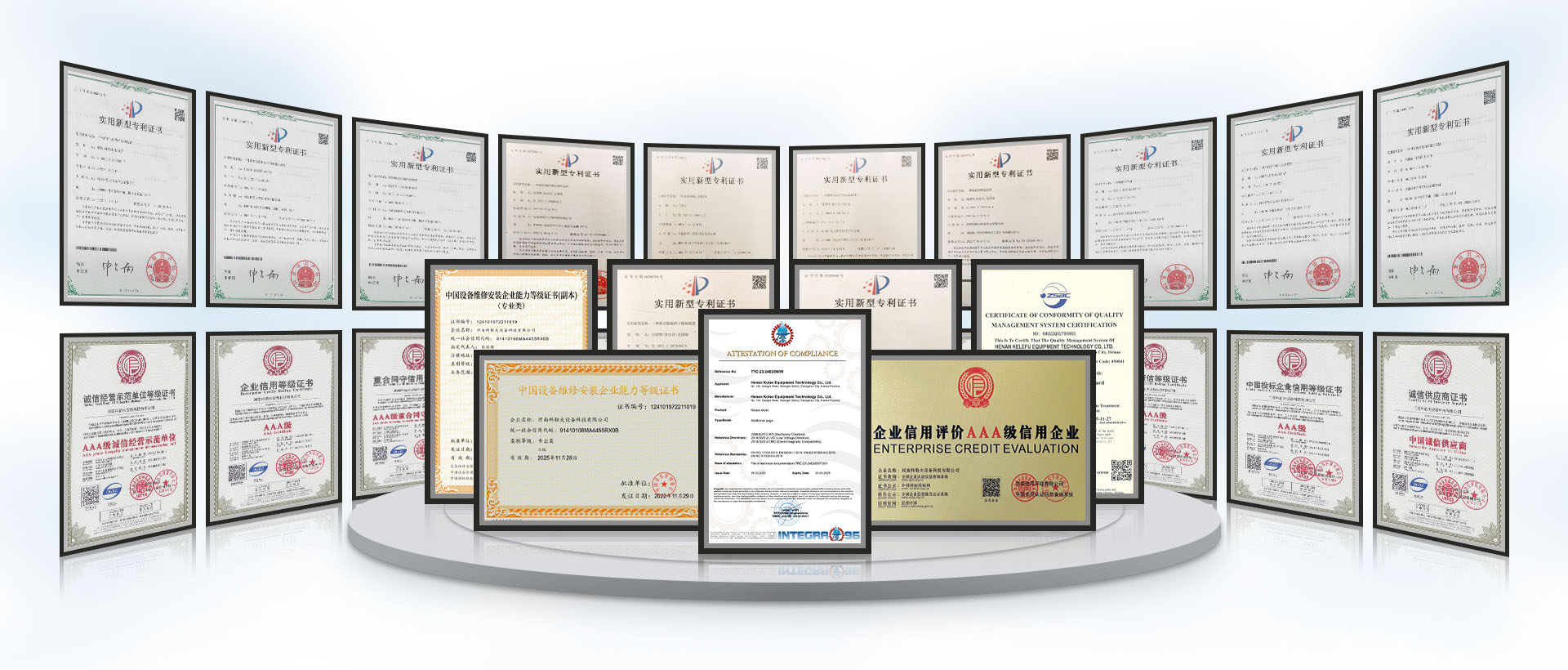